nec 310-16 table pdf
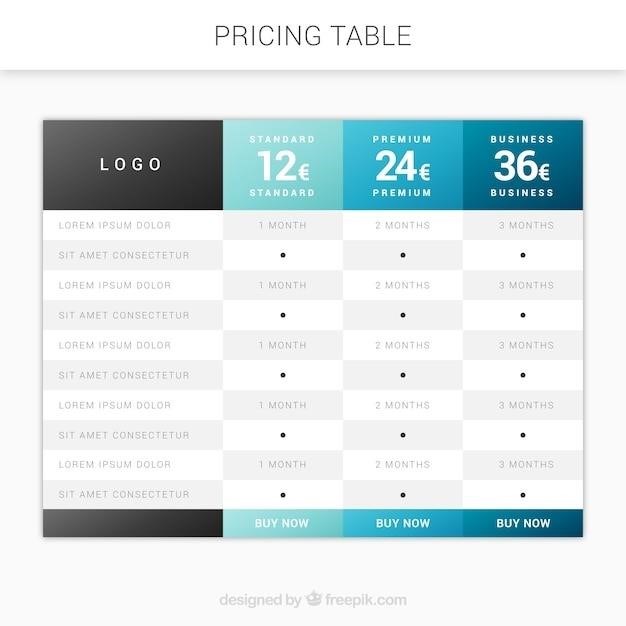
NEC Table 310․16⁚ A Comprehensive Overview
NEC Table 310․16, also known as Table 310․15(B)(16), provides a comprehensive guide to the allowable ampacities of insulated conductors rated up to 2000 volts․ This crucial table, found within the National Electrical Code (NEC), is a cornerstone for safe and efficient electrical system design․ The table outlines the maximum current carrying capacity of various conductor sizes and materials, including copper, aluminum, and copper-clad aluminum, under different temperature conditions․ It’s a valuable resource for electricians, engineers, and anyone involved in electrical installations․
Introduction to NEC Table 310․16
NEC Table 310․16, formally known as Table 310․15(B)(16) in the 2011 and subsequent editions of the National Electrical Code (NEC), serves as a fundamental reference for determining the allowable ampacity of insulated conductors․ This table, located within Article 310 of the NEC, provides a detailed breakdown of the maximum current-carrying capacity for various conductor types, sizes, and temperature ratings․ It is a vital tool for electricians, engineers, and anyone involved in electrical system design and installation, ensuring safe and efficient operation․ The table’s significance lies in its role in preventing overheating and potential fire hazards by ensuring that the conductors used in an electrical system are appropriately sized to handle the current flow․
History and Evolution of Table 310․16
NEC Table 310․16 has undergone a significant evolution throughout its history, reflecting advancements in electrical technology, safety practices, and industry standards․ Initially introduced as Table 310․16 in earlier editions of the NEC, it underwent a renumbering and restructuring in the 2011 NEC, becoming Table 310․15(B)(16)․ This change was part of a broader reorganization within the NEC, aimed at improving clarity and consistency․ Despite the change in designation, the table’s core purpose of providing ampacity ratings for insulated conductors remained unchanged․ Over time, updates to the table have incorporated new conductor types, materials, and temperature ratings, reflecting the ever-evolving landscape of electrical systems․ The table’s ongoing evolution ensures its relevance and effectiveness in safeguarding electrical installations․
Key Parameters and Conditions
NEC Table 310․16 is built upon a foundation of key parameters and conditions that govern the ampacity ratings it provides․ These parameters ensure the table accurately reflects the safe current-carrying capacity of conductors under specific circumstances․ The table focuses on insulated conductors rated between 0 and 2000 volts, operating within a temperature range of 60°C to 90°C (140°F to 194°F)․ A crucial aspect is the assumption of a 30°C (86°F) ambient temperature, representing a standard environmental condition for electrical installations․ The table also specifies that the ampacity ratings apply to scenarios where no more than three current-carrying conductors are present within a raceway, cable, or directly buried in the earth․ Understanding these parameters is essential for correctly applying the table’s data and ensuring safe and compliant electrical installations․
Ampacity Ratings for Different Conductor Types
NEC Table 310․16 provides a comprehensive breakdown of ampacity ratings for various conductor types, taking into account their size and material․ The table offers distinct columns for copper, aluminum, and copper-clad aluminum conductors, allowing for direct comparison of their current-carrying capacities․ Each column lists the ampacity for different conductor sizes, ranging from small AWG gauges to larger kcmil sizes․ The ampacity values are presented for different temperature ratings of the conductor insulation, typically 60°C, 75°C, and 90°C․ This allows for selecting the appropriate conductor size based on the intended application and the expected operating temperature․ The table’s detailed information on ampacity ratings for different conductor types is crucial for ensuring safe and efficient electrical installations, considering the specific needs of each project․
Copper Conductors
NEC Table 310․16 provides detailed information on the ampacity of copper conductors, which are widely used in electrical installations due to their excellent conductivity․ The table lists ampacity values for various sizes of copper conductors, ranging from small AWG gauges like 14 AWG to larger kcmil sizes․ These values are presented for different temperature ratings of the conductor insulation, typically 60°C, 75°C, and 90°C․ The ampacity of copper conductors is influenced by factors such as the conductor size, insulation temperature rating, and the number of conductors in a raceway․ For instance, a 14 AWG copper conductor with 60°C insulation has an ampacity of 20 amps, while a 12 AWG copper conductor with 75°C insulation can handle 25 amps․ This information is crucial for selecting the appropriate size of copper conductor for a specific application, ensuring safe and efficient electrical installations․
Aluminum Conductors
NEC Table 310․16 also includes ampacity ratings for aluminum conductors, which are often used in electrical systems due to their cost-effectiveness and lightweight nature․ The table provides ampacity values for various sizes of aluminum conductors, similar to copper conductors, ranging from smaller AWG gauges to larger kcmil sizes․ These values are presented for different temperature ratings of the conductor insulation, typically 60°C, 75°C, and 90°C․ It’s important to note that aluminum conductors have a lower ampacity than copper conductors of the same size due to their slightly lower conductivity․ Therefore, when using aluminum conductors, it’s essential to select a larger size to ensure adequate current carrying capacity․ For example, a 12 AWG aluminum conductor with 75°C insulation has an ampacity of 20 amps, compared to the 25 amps for a 12 AWG copper conductor with the same insulation․ Understanding these differences is crucial for selecting the appropriate size of aluminum conductor for a particular application․
Copper-Clad Aluminum Conductors
NEC Table 310․16 also includes ampacity ratings for copper-clad aluminum conductors, which combine the cost-effectiveness of aluminum with the superior conductivity of copper․ These conductors feature an aluminum core, providing strength and durability, with a thin copper cladding that enhances electrical conductivity․ The table provides ampacity values for copper-clad aluminum conductors in the same columns as aluminum conductors, reflecting their similar electrical characteristics․ The ampacities for copper-clad aluminum conductors are generally higher than those for aluminum conductors of the same size, reflecting the improved conductivity provided by the copper cladding․ However, it’s important to note that the ampacities for copper-clad aluminum conductors are still lower than those for solid copper conductors of the same size․ Understanding these differences is crucial for selecting the appropriate size of copper-clad aluminum conductor for a particular application․
Factors Affecting Ampacity
The ampacity values presented in NEC Table 310․16 are based on a standard set of conditions, including an ambient temperature of 30°C (86°F)․ However, various factors can influence the actual ampacity of a conductor in a real-world installation․ These factors must be considered when determining the appropriate conductor size for a given application․ One significant factor is the ambient temperature, which can vary significantly depending on the environment and the time of year․ Higher ambient temperatures can reduce the ampacity of conductors due to increased heat dissipation․ Additionally, the number of conductors installed in a raceway or cable can impact ampacity․ As the number of conductors increases, the heat generated by each conductor can affect the others, leading to a reduction in overall ampacity․ The method of installation, such as whether conductors are installed in a raceway, conduit, or directly buried, also influences ampacity․ Conductors installed in a raceway or conduit can experience higher temperatures due to heat buildup, requiring a lower ampacity rating compared to those installed in free air or directly buried․ Understanding these factors is crucial for ensuring that conductors are properly sized to handle the intended current load while maintaining safe operating temperatures․
Ambient Temperature
Ambient temperature is a critical factor that directly affects the ampacity of conductors, as outlined in NEC Table 310․16․ The table’s values are based on a standard ambient temperature of 30°C (86°F)․ However, real-world conditions often deviate from this standard, necessitating adjustments to the ampacity values․ Higher ambient temperatures can significantly reduce the ampacity of conductors due to increased heat dissipation․ As the ambient temperature rises, the conductor’s temperature also increases, potentially exceeding its safe operating limit․ The NEC provides correction factors for adjusting ampacity based on the actual ambient temperature․ These correction factors are applied to the ampacity values listed in Table 310․16 to account for the impact of higher or lower ambient temperatures․ For example, if the ambient temperature is 40°C (104°F), the ampacity of a conductor may need to be reduced by a certain percentage to ensure safe operation․ Therefore, understanding the actual ambient temperature and applying the appropriate correction factors is crucial for determining the accurate ampacity of a conductor in a given installation․
Number of Conductors
The number of conductors within a raceway, cable, or directly buried installation significantly influences the ampacity of each conductor․ NEC Table 310․16, specifically, focuses on the allowable ampacities for situations with “Not More Than Three Current-Carrying Conductors․” This limitation is crucial for managing heat buildup within the confined space․ When multiple conductors are bundled together, heat generated by each conductor can affect the others, leading to increased overall temperature․ This increased temperature can reduce the ampacity of each conductor, limiting the amount of current they can safely carry․ NEC Table 310․16 provides ampacity values based on the assumption of three or fewer conductors, but for installations with more than three conductors, adjustments are required․ The NEC includes correction factors to account for the increased heat buildup and the resulting reduction in ampacity․ These correction factors are applied to the ampacity values listed in Table 310․16 to ensure that the overall heat generated by the multiple conductors remains within safe limits․
Installation Methods
The method used to install conductors, whether in raceways, cables, or directly buried in the earth, directly impacts their ampacity․ NEC Table 310․16, specifically, focuses on situations where conductors are either within raceways, cables, or directly buried․ These installation methods present unique thermal considerations that influence the ampacity of the conductors․ For instance, conductors within raceways are more likely to experience higher temperatures due to the confined space and heat generated by other conductors․ The same applies to cables, where multiple conductors are bundled together․ Directly buried conductors, on the other hand, are exposed to the ambient temperature of the surrounding soil, which may fluctuate․ The NEC acknowledges these differences by providing different ampacity values depending on the installation method․ For example, the ampacity values for conductors in raceways or cables may be lower than those for conductors buried directly in the earth, reflecting the greater potential for heat buildup in the former․ These adjustments in ampacity ensure that conductors are properly sized for their specific installation environment, minimizing the risk of overheating and ensuring safe electrical operation․
Applications of NEC Table 310․16
NEC Table 310․16 is a vital tool across a wide range of electrical applications, ensuring safe and efficient wiring practices․ Its applications extend from residential wiring, where it guides the selection of appropriate wire sizes for common household circuits, to complex commercial and industrial installations, where it helps determine the capacity of feeders and branch circuits supplying high-power equipment․ The table also plays a crucial role in the design of solar energy systems, where it’s used to select the correct wire sizes for connecting photovoltaic panels, inverters, and other system components․ This ensures that these systems can handle the current flow generated by solar panels without overheating or compromising safety․ The versatility of NEC Table 310․16 makes it an indispensable resource for electricians, engineers, and anyone involved in electrical system design, regardless of the scale or complexity of the project․
Residential Wiring
NEC Table 310․16 is a cornerstone for safe and efficient residential wiring, ensuring that homes are equipped with electrical systems that can handle the demands of modern appliances and devices․ The table provides clear guidance on the appropriate wire sizes for various circuits, such as those powering lights, outlets, and appliances, based on their current draw․ For instance, when wiring a circuit for a high-power appliance like an electric stove, the table helps electricians determine the correct wire size to prevent overheating and potential fire hazards․ This ensures that circuits are adequately sized to handle the load, promoting safety and preventing overloads that could lead to damage or electrical fires․ The table also guides the selection of wire sizes for outlets and lighting circuits, ensuring that they can handle the current demands of various devices and fixtures․ This is essential for a safe and functional electrical system in any home․
Commercial and Industrial Applications
NEC Table 310․16 plays a crucial role in ensuring the safety and efficiency of electrical systems in commercial and industrial settings․ These environments often involve higher power demands compared to residential applications, requiring careful consideration of conductor sizing to prevent overheating and potential hazards․ The table guides the selection of appropriate wire sizes for various electrical systems, including those powering heavy machinery, large lighting systems, and complex electrical equipment․ For example, in a factory setting, the table helps determine the correct wire size for motors driving production lines, ensuring that they can handle the high currents without overheating․ Similarly, in large commercial buildings, the table guides the selection of wire sizes for HVAC systems, ensuring that they can deliver power reliably and safely․ The table also helps in the design of distribution panels and feeder circuits, ensuring that they can handle the substantial power demands of commercial and industrial operations․ By adhering to the guidelines outlined in Table 310․16, electricians and engineers can create safe and efficient electrical systems that meet the unique needs of these demanding environments․
Solar Energy Systems
The rise of solar energy systems has created a significant demand for accurate and reliable ampacity information, and NEC Table 310․16 plays a vital role in this domain․ Solar panels generate direct current (DC) electricity, which is then converted to alternating current (AC) for use in homes and businesses․ The wiring connecting solar panels to inverters and distribution panels is critical for safe and efficient energy transfer․ NEC Table 310․16 provides the necessary guidance for selecting the correct wire sizes for solar array wiring, ensuring that they can handle the DC currents generated by the panels without overheating․ This table helps determine the appropriate wire sizes for both the positive and negative conductors of the solar array circuit, ensuring that the system operates safely and efficiently․ Furthermore, the table is crucial for determining the ampacity of the conductors connecting the inverter to the main electrical panel, ensuring that the system can deliver the generated power safely and reliably to the grid or the home․ By adhering to the guidelines outlined in Table 310․16, electricians and solar installers can create safe and efficient solar energy systems that contribute to a sustainable future․
Importance of Compliance
Compliance with NEC Table 310․16 is paramount for ensuring the safety and reliability of electrical systems․ By adhering to the ampacity guidelines outlined in this table, electricians and engineers can prevent overheating and potential fires caused by overloaded conductors․ Oversized conductors may seem wasteful, but they contribute to a more efficient system by minimizing voltage drop, ensuring that electrical equipment receives the necessary power to operate properly․ The NEC mandates compliance with Table 310․16 for a reason—it is a safety standard established to protect life and property․ Failure to comply can result in fines, insurance claim denials, and, most importantly, potential injury or death․ The consequences of non-compliance can be severe, emphasizing the importance of following the guidelines outlined in this table․ Furthermore, compliance with NEC Table 310․16 promotes a consistent and reliable electrical infrastructure․ It ensures that all electrical installations meet a minimum standard, reducing the risk of malfunctioning systems and improving overall safety․